Porosity in Welding: Identifying Common Issues and Implementing Ideal Practices for Prevention
Porosity in welding is a pervasive issue that usually goes undetected until it creates considerable troubles with the integrity of welds. In this conversation, we will certainly check out the crucial aspects adding to porosity formation, analyze its damaging effects on weld performance, and go over the finest practices that can be taken on to lessen porosity incident in welding processes.
Usual Reasons For Porosity

An additional frequent perpetrator behind porosity is the presence of impurities on the surface area of the base metal, such as oil, grease, or corrosion. When these contaminants are not efficiently removed before welding, they can evaporate and end up being entraped in the weld, causing flaws. Moreover, using filthy or wet filler products can present contaminations into the weld, adding to porosity concerns. To alleviate these common sources of porosity, comprehensive cleansing of base metals, appropriate securing gas option, and adherence to optimal welding specifications are essential methods in achieving top notch, porosity-free welds.
Impact of Porosity on Weld Quality

The visibility of porosity in welding can considerably endanger the structural stability and mechanical homes of welded joints. Porosity develops spaces within the weld metal, deteriorating its total strength and load-bearing capability.
Welds with high porosity levels tend to display lower effect strength and decreased capacity to deform plastically before fracturing. Porosity can restrain the weld's capacity to successfully transfer forces, leading to early weld failure and potential safety and security risks in crucial structures.
Ideal Practices for Porosity Prevention
To enhance the architectural integrity and high quality of bonded joints, what details measures can be implemented to decrease the incident of porosity throughout the welding process? Porosity prevention in welding is crucial to make sure the honesty and strength of the last weld. One reliable practice is proper cleansing of the base metal, removing any kind of contaminants such as rust, oil, paint, or moisture that might cause gas entrapment. Making certain that the welding equipment is in good condition, with content clean consumables and proper gas flow rates, can likewise significantly decrease porosity. Furthermore, preserving a steady arc and managing the welding specifications, such as voltage, present, and take a trip rate, aids develop a regular weld swimming pool that lessens the danger of gas entrapment. Making use of the appropriate welding method for the specific material being welded, such as adjusting the welding angle and weapon placement, can better stop porosity. Routine inspection of welds and prompt remediation of any kind of concerns recognized throughout the welding process are vital methods to avoid porosity and produce top quality welds.
Importance of Appropriate Welding Strategies
Carrying out correct welding strategies is critical in making sure the structural stability and top quality of welded joints, building upon the foundation of efficient porosity avoidance actions. Excessive warm can lead to boosted porosity due to the entrapment of gases in the weld swimming pool. Additionally, using the suitable welding specifications, such as voltage, existing, and take a trip speed, is essential for accomplishing audio welds with marginal porosity.
In addition, the choice of welding process, whether it be MIG, TIG, or stick welding, ought to line up with the certain needs of the task to make certain optimum results. Proper cleaning and preparation of the base metal, in addition to choosing the appropriate filler product, are additionally crucial parts of proficient welding techniques. By adhering to these best practices, welders can decrease the risk of porosity formation and create high-grade, structurally sound welds.
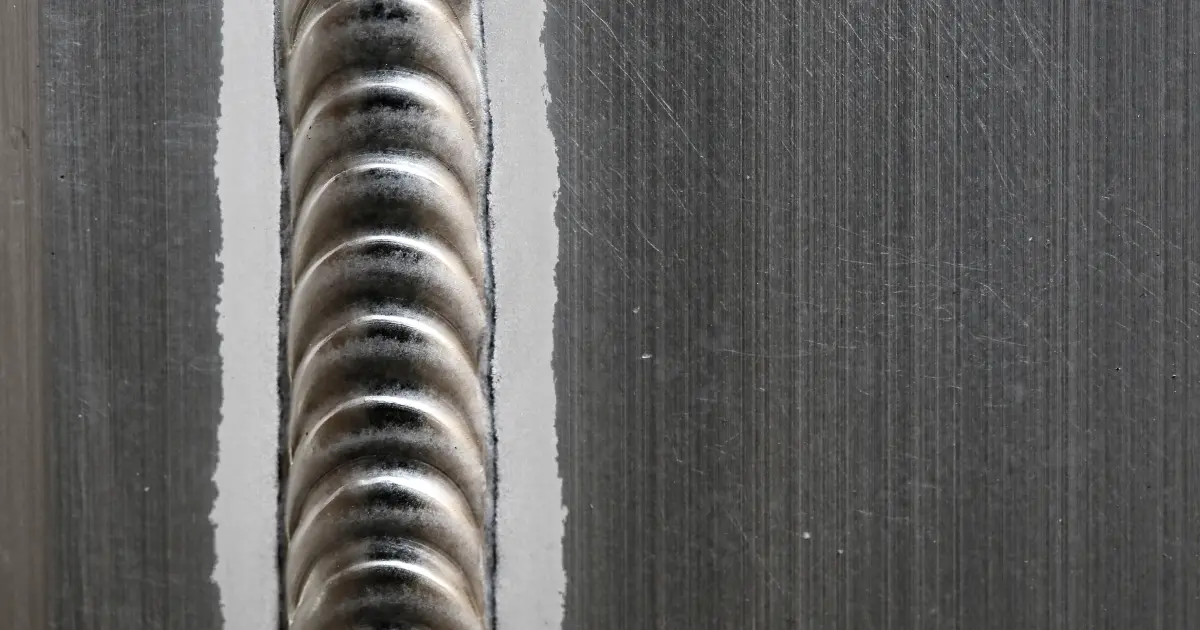
Testing and Quality Assurance Steps
Quality assurance steps play a critical role in confirming the honesty and integrity of bonded joints. Testing procedures are vital to identify and avoid porosity in welding, guaranteeing the stamina and sturdiness of the check final product. Non-destructive testing methods such as ultrasonic testing, radiographic testing, and aesthetic examination are generally used to recognize possible flaws like porosity. These methods enable for the assessment of weld quality without compromising the honesty of the joint. What is Porosity.
Conducting pre-weld and post-weld assessments is also important in preserving quality assurance requirements. Pre-weld assessments involve confirming the materials, devices setups, and tidiness of the workspace to avoid contamination. Post-weld evaluations, on the other hand, evaluate the final weld for reference any kind of flaws, consisting of porosity, and verify that it satisfies specified standards. Carrying out a comprehensive high quality control strategy that includes detailed testing procedures and examinations is critical to minimizing porosity concerns and ensuring the overall quality of welded joints.
Verdict
In verdict, porosity in welding can be a common concern that influences the top quality of welds. By identifying the common sources of porosity and implementing best methods for prevention, such as appropriate welding strategies and screening actions, welders can ensure premium quality and dependable welds. It is vital to focus on avoidance techniques to lessen the event of porosity and keep the stability of welded structures.